- Is a Wash & Cure Station Worth It? Creality UW-03 Review - April 29, 2024
- Z Seam | How to Hide & Avoid | Cura & PrusaSlicer - April 20, 2024
- Qidi Tech Q1 Pro – Best Orca Slicer Settings & Profile - April 9, 2024
Disclosure: Links marked with * are Affiliate Links. I earn from qualifying purchases if you decide to make a purchase through these links – at no additional cost for you!
If you are looking for a 3D printer, sooner or later you will have to decide between a Bowden extruder and a direct drive extruder. Both systems have their advantages and disadvantages and are suitable for different requirements.
A Bowden extruder sits on the frame of the 3D printer. This makes the print head lighter and allows it to reach higher print speeds. A direct drive extruder sits directly in the print head, improving extrusion accuracy and enabling the processing of flexible filaments.
In this article, I will introduce you to both extruder systems in detail, demonstrate their respective designs, how they work, and give you the answer to which extruder is best for you.
However, before we get into the details, here’s a quick summary of when either a Bowden extruder or a direct drive extruder is worthwhile:
Extruder | Bowden | Direct |
---|---|---|
Speed | High | Medium |
Print quality | Good | Very good, with fewer printing errors |
Filaments | Rigid filaments: PLA ABS PETG | Rigid & Flexible Filaments: PLA ABS PETG TPU |
Table of Contents:
Design & Function
Bowden Extruder
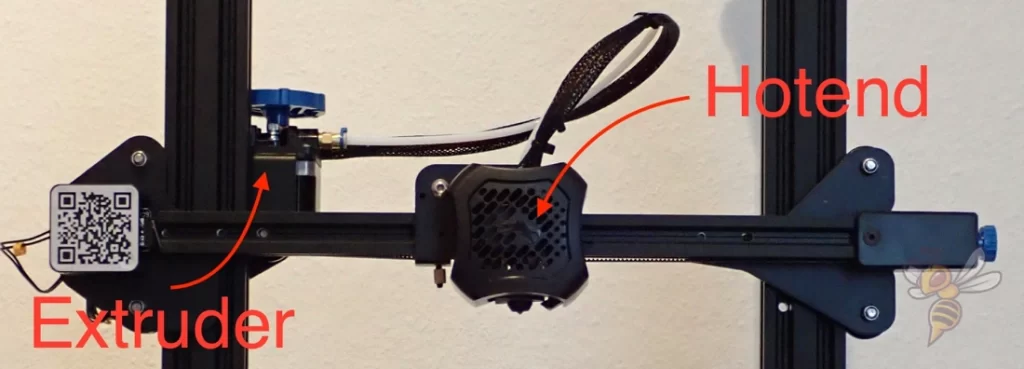
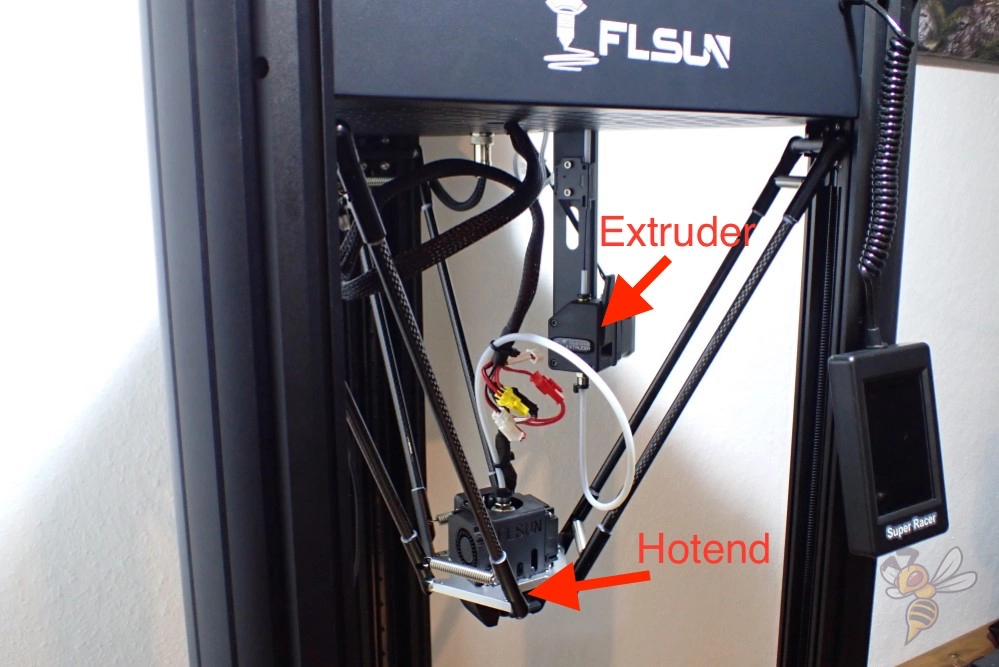
A Bowden extruder sits far away from the print head on the frame or on an axis of the 3D printer. The filament is transported from the extruder through a PTFE tube to the print head.
Because the extruder is not integrated into the print head in a Bowden system, the print head is generally smaller and lighter overall than in a direct drive system.
Due to the lower weight, higher speeds can be achieved and the smaller size of the print head allows a slightly larger print volume in the z-direction.
Since the filament has to travel a longer distance to the hot nozzle and there is friction in the PTFE tubing, the motors that drive the extruder must be somewhat stronger than with a direct drive extruder. However, the motors may be larger and heavier here, since they are not located in the print head and do not influence the weight of the print head.
Direct Drive Extruder
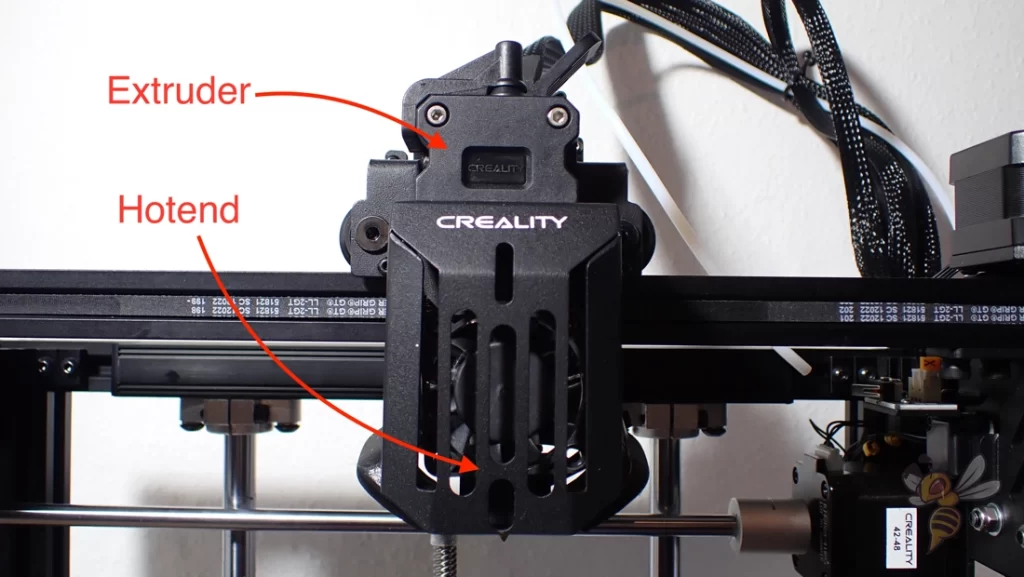
With a direct drive extruder, the extruder is located in the print head. The filament only has to travel a short distance from the extruder to the hot nozzle.
The print head is usually larger and heavier when the extruder is built directly into the print head. Meanwhile, the line between these two extruder systems is blurring in terms of their size and weight.
Some time ago, direct drive extruders were hardly worthwhile, as they made the print head extremely heavy and large. Nowadays, however, there are more and more direct drive systems that can keep up with the low weight and small size of print heads from Bowden systems.
An example of this would be the Sprite direct drive extruder of the Ender 3 S1. The print head is as light and small as some Bowden systems.
Print Speed
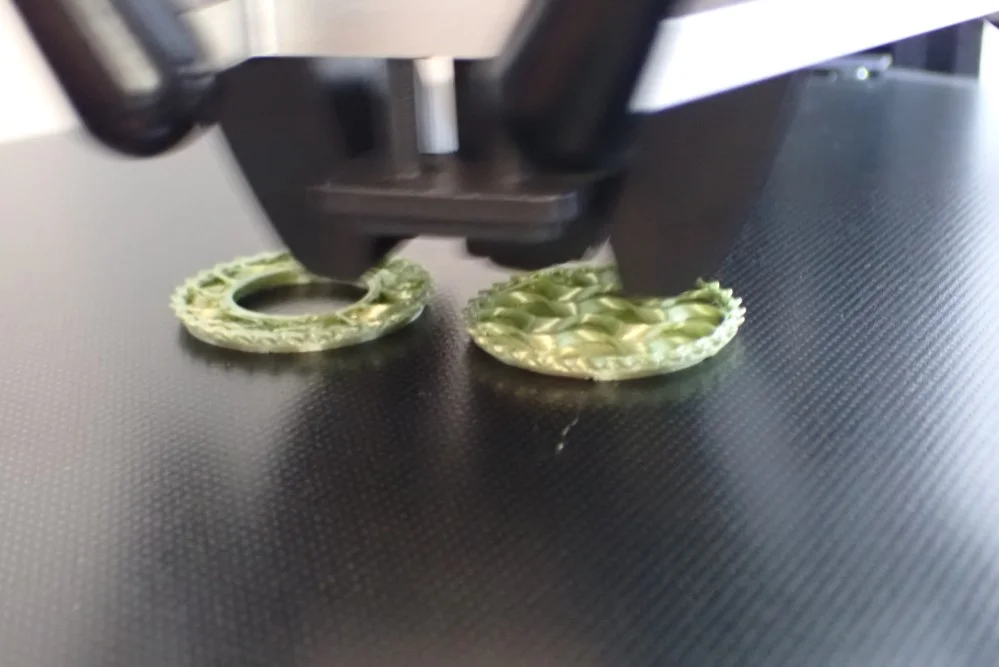
3D printers with Bowden extruders typically achieve higher print speeds than 3D printers with direct drive extruders. This is due to the weight of the print heads.
Heavy print heads or an unstable design can cause vibrations at high speeds, resulting in ringing or ghosting.
The maximum print speed at which error-free printing is possible therefore depends on the weight of the print head in addition to a stable design. While there are exceptions, most print heads with direct drive extruders are heavier than those on a 3D printer with a Bowden extruder.
Therefore, 3D printers with a Bowden extruder can usually achieve a higher print speed than those with a direct drive extruder.
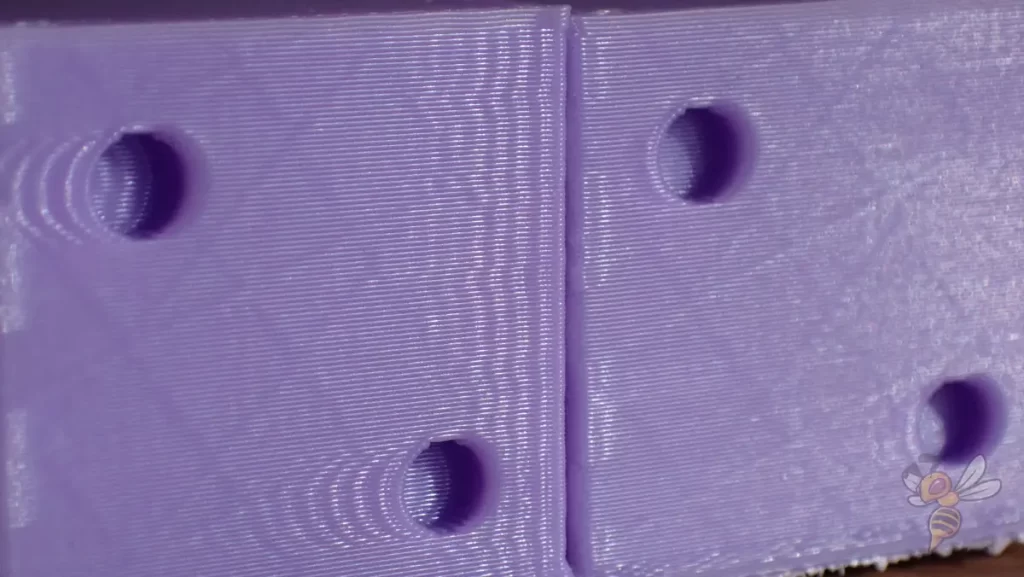
In addition to the designs, however, the choice of firmware can also influence the print speed. For example, Klipper can use an acceleration sensor on the print head to measure and compensate for the accelerations that occur during direction changes.
You can use the firmware on 3D printers with a Bowden or direct drive extruder. In both cases, the print speed is increased significantly without having to accept a poorer print quality.
If you’re curious, you can read my hands-on test of the Creality Sonic Pad, which allowed me to print flawlessly at an incredibly fast 250 mm/s (it was only 60 mm/s without the pad!).
Response Time
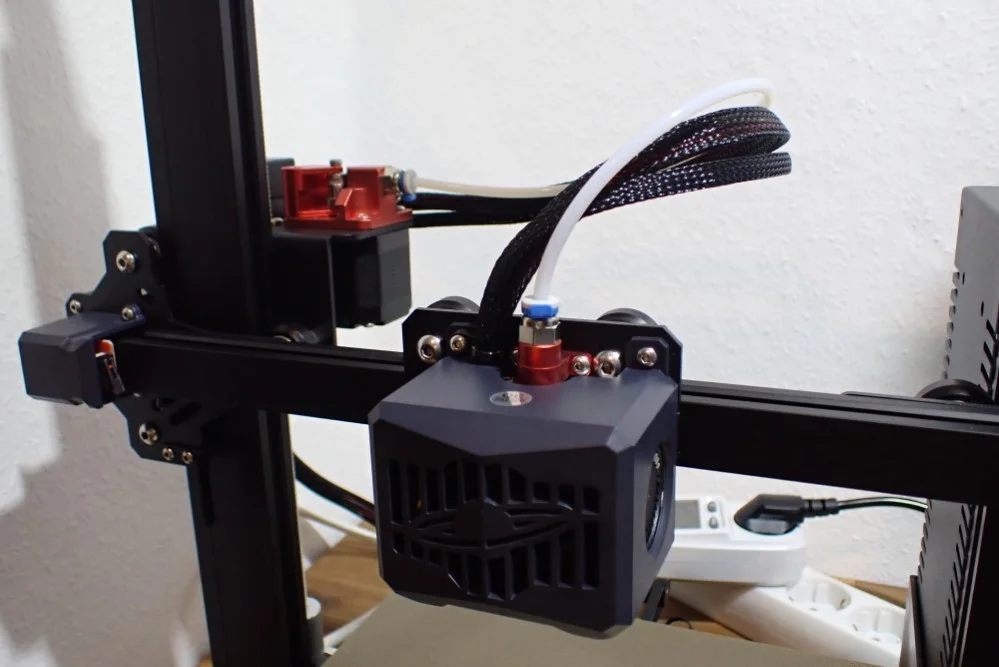
The further the extruder is from the hot nozzle, the more the extrusion and retraction movements get delayed. Therefore, direct drive extruders print more accurately and with fewer print errors than systems with a Bowden extruder.
There are basically three factors that influence the reaction time of extrusion and retraction:
Filament flexibility: Flexible filaments can partially compensate for the movements of the extruder. During extrusion movements, they compress and thus delay the feed. During retraction movements, they stretch and thus delay the retraction.
The longer the distance between the extruder and the nozzle, the stronger this effect becomes. More about this in the next section on compatible filaments.
PTFE tube tolerance: In a Bowden extruder, the filament gets pushed from the extruder to the print head through a PTFE tube. If the inner diameter of the PTFE tubing is much larger than the diameter of the filament, the filament can flap back and forth in the tubing during extrusion and retraction motions and have a delayed response. This is why high quality PTFE tubing is a popular upgrade for 3D printers using Bowden extruders.
Friction of the filament in the PTFE tubing: The inside of the PTFE tubing of a Bowden extruder should be as smooth as possible to prevent friction to the filament. The greater the friction, the greater the delay in movement.
Filaments
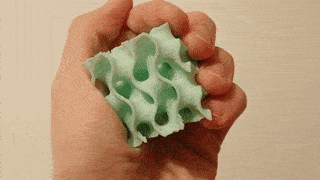
The longer the distance between the extruder and the nozzle, the more flexible filaments can compensate for the extrusion and retraction movements of the extruder. Therefore, Bowden extruders can only process flexible filaments with difficulty or not at all, whereas direct drive extruders can.
To illustrate this effect, I created a GIF for each of the extrusion and retraction motion. You can see the non-existent delay for a rigid filament like PLA, the large delay for a flexible filament like TPU on a Bowden extruder, and the small delay for TPU on a direct drive extruder.
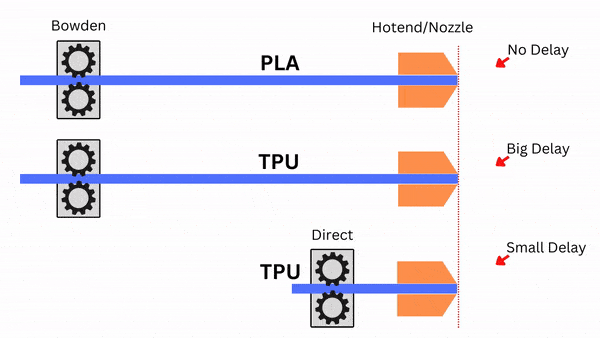
When a flexible filament such as TPU is pushed through the long PTFE tube by a Bowden extruder, it is compressed along the path between the extruder and the nozzle before the movement reaches the nozzle. With a direct drive extruder, the effect also occurs, but the delay is much smaller.
Printing defects that can occur as a result include holes, a strong Z-seam or other phenomena of under-extrusion at the beginning of a layer.
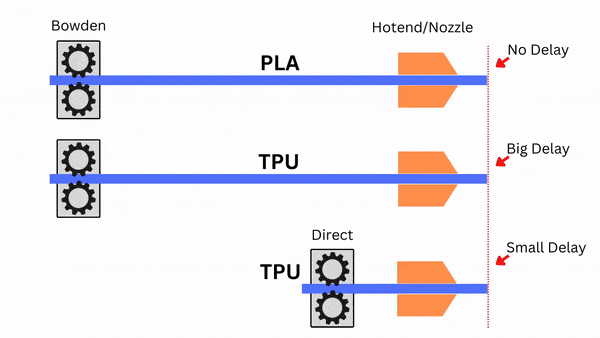
With retraction, the flexible filament is stretched between the extruder and the nozzle before the movement arrives at the end of the filament. The filament is therefore pulled back into the nozzle a certain amount of time later than it should have been.
This effect is much greater with Bowden extruders than with direct drive extruders. This is the main reason why Bowden extruders are hardly or not at all suitable for flexible filaments.
The print error, which is predominantly caused by this delay in retraction, is stringing. With strong delays, even blobs can occur.
Although it is sometimes almost impossible to correct these print errors with Bowden extruders, 3D printers with direct drive extruders also require more effort to calibrate the retraction than rigid filaments.
Filament Sensor
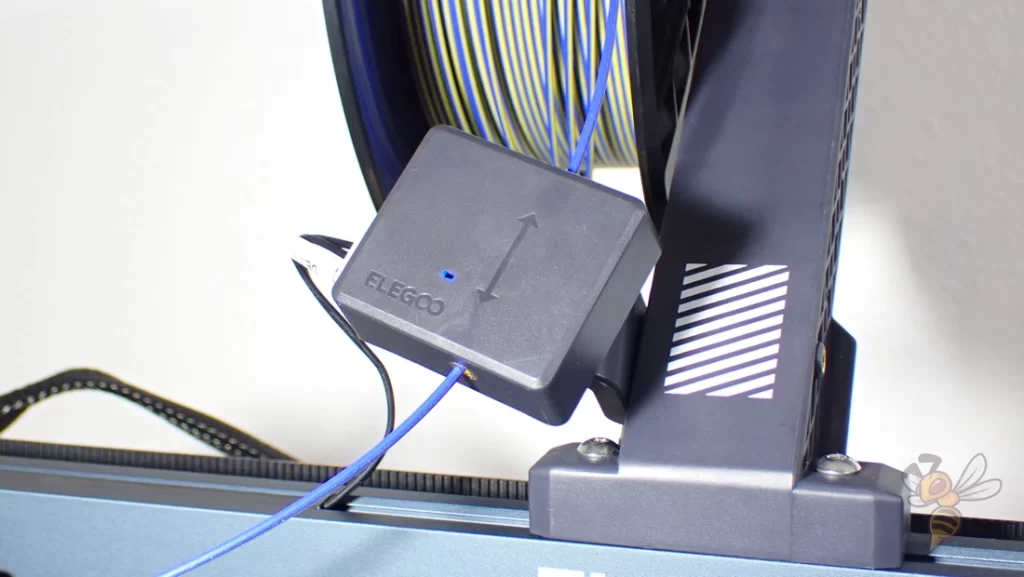
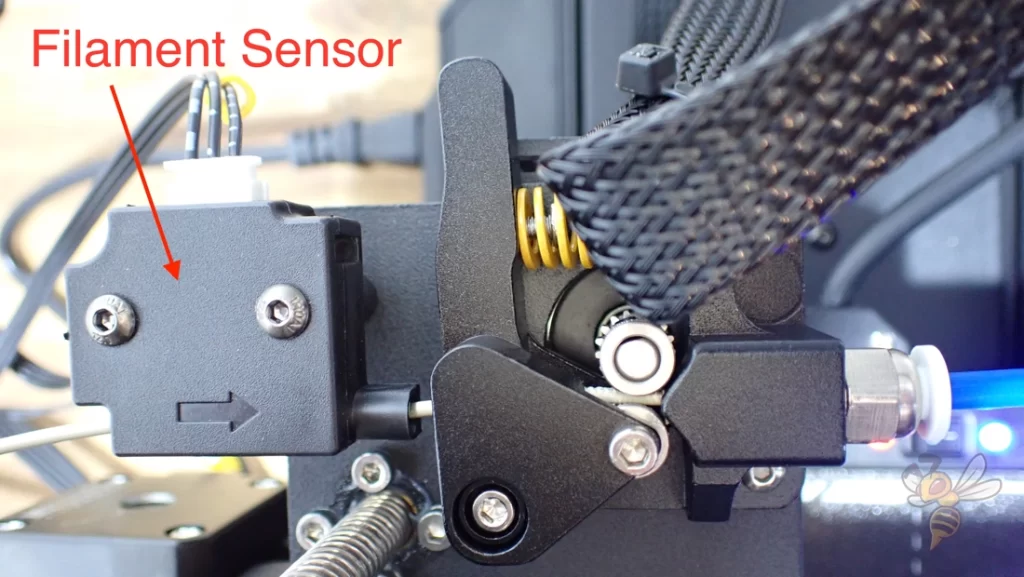
A filament sensor detects broken or used filament. For 3D printers with Bowden extruders, the filament sensor is located in front of the extruder. For 3D printers with direct drive extruders, the filament sensor is located either under the filament holder or in the print head.
The filament sensor must be positioned before the extruder in both cases. In a 3D printer with a Bowden extruder, positioning is generally easier because the extruder is mounted in a stable location on the frame or an axis. There, the additional weight of a filament sensor is no problem.
Placing the filament sensor on a 3D printer with a direct drive extruder is a bit more difficult because the extruder moves with the print head. There are also print heads that are so compact that the filament sensor still has room inside the print head.
Typically, however, the filament sensor is mounted outside the print head to save weight. Newer 3D printers have free-swinging variants mounted directly under the filament holder at the upper end of the frame.
3D Printer Examples
Bowden extruder 3D Printers:
Direct drive extruder 3D Printers:
Conclusion: Which Extruder System is Better?
Objectively speaking, neither extruder system is better than the other. Depending on your requirements and intended use, a Bowden or direct drive extruder may be more worthwhile for you.
If you mainly want to process rigid filaments, a Bowden extruder is absolutely sufficient thanks to its higher printing speeds.
If you intend to work with flexible filaments, you should choose a 3D printer with a direct drive extruder. The print quality is also somewhat higher with these extruders.
Disclosure: This website is the property of Martin Lütkemeyer and is operated by Martin Lütkemeyer. Martin Lütkemeyer is a member of the Amazon Services LLC and other Affiliate Programs. These are affiliate advertising programs designed to enable websites to earn advertising revenue through advertising and linking to Amazon.com and others. Links marked with * are affiliate links.