- Printing BIG with the JUPITER SE – A Review - May 13, 2024
- Is a Wash & Cure Station Worth It? Creality UW-03 Review - April 29, 2024
- Z Seam | How to Hide & Avoid | Cura & PrusaSlicer - April 20, 2024
Disclosure: Links marked with * are Affiliate Links. I earn from qualifying purchases if you decide to make a purchase through these links – at no additional cost for you!
With 3D printing, three-dimensional objects can be produced layer by layer in one piece. What is special about 3D printing is that this technology allows geometries to be implemented that are not possible with other manufacturing processes.
Also, the speed of production is far superior to most other manufacturing processes. Therefore, 3D printing is already widely used in both the private and industrial sectors.
This article is intended to provide an overview of 3D printing technology and give beginners an easy introduction to the subject. We’ll take a look at each 3D printing technology, what applications they have right now, and how a 3D printing process works in detail.
By the end of the article, you’ll have a good overview of 3D printing and its applications and know which of the 3D printing technologies is right for you.
If you are interested in the hobby of 3D printing and want to bypass the theoretical stuff, you should read this article: How to Get Started with 3D Printing | Beginner’s Guide
Table of Contents:
Brief History of 3D Printing

The first ideas for 3D printing came very early in the 1940s and 1950s. As with many other modern technologies, the first ideas for 3D printing originated in science fiction stories.
However, the first 3D printers that were successfully used were not developed until the 1980s. These devices were very expensive, however, and the technology was still in its infancy and in research.
The most common technologies today, FDM and SLA 3D printing, were also patented in the 1980s. Chuck Hull is one of the inventors of SLA 3D printing and filed his patent for it in 1984. S. Scott Crump filed his patent for FDM 3D printing in 1989.
Since the respective patents have expired, manufacturers can use these technologies without paying royalties. This has created a market for inexpensive 3D printers and thus spread 3D printing exponentially in all fields.
How Does 3D Printing Work?
Steps in the 3D Printing Process

No matter what 3D printing technology it is, the steps in the printing process are always the same. In the beginning, after the idea is created, a digital file of the object is prepared for printing in a suitable 3D printing software.
After that, the object is manufactured using the chosen 3D printing method and may still need to be reworked afterwards.
STL File

An STL (stereolithography) file is a widely used format in 3D printing. Other formats that are popularly used for 3D printing are OBJ and 3MF.
An STL file describes the surface of an object using many small triangles. This type of three-dimensional representation of an object can be read by most programs for 3D printing.
All common CAD programs can generate STL files and are thus suitable for 3D printing. For home use, browser-based programs like TinkerCAD and more professional programs like Fusion360 are popular.
In the private sector, it is common to use the objects of others so that you don’t have to create 3D objects yourself. For this purpose, there are numerous portals where such objects are shared and offered. Examples of such portals are Thingiverse, Cults3D or MyMiniFactory.
Once you have finished designing the object or downloaded a finished object from one of the websites, you can prepare it for 3D printing in a so-called slicer.
Slicing

The programs that convert the STL files in 3D printing into a language that 3D printers can understand are called slicers. Their name comes from the fact that they slice the object into many small layers that are printed step by step by the 3D printer.
In a slicer, important properties of the object are determined, such as the layer height and density. The smaller the layer height, the finer the surface. Especially in FDM 3D printing, this is a classic feature by which a 3D-printed object can be recognized.
Through the code generated by the slicer, the 3D printer knows where and when to deposit the material. That’s why most 3D printing technologies have their own slicers, as some of the commands differ greatly.
If you are looking for a quick start into 3D printing, I can recommend Cura for FDM 3D printers and ChiTuBox for resin 3D printers. These two programs are the most popular slicers for the respective printing technologies, offer an easy start and can also be configured in detail, so they are also interesting for professionals.
After slicing, the finished code can be brought to the 3D printer. This is done either by cable directly from the PC or via a suitable data carrier.
3D Printing

Depending on which 3D printing technology is used, the 3D printer must be prepared before printing. Most often this consists of loading material (filament/resin/powder/etc.) and heating the print bed. The print bed is the surface on which the object is printed layer by layer.
The individual layers are printed on top of each other until the object is finished. In a sense, the layers are added together, which is why 3D printing is also called additive manufacturing.
The great advantage of 3D printing is its speed. Most objects are printed within a few hours and a few days at most. With most 3D printing technologies, this time is pure waiting time, as the 3D printer runs independently. Complex geometry can be produced in one piece without the need for additional steps.
After printing, the finished object may need some post-processing. Depending on the technology, the object may still need to be cured, and any protruding material residue or support structures may need to be removed.
With most 3D printing technologies, overhangs can only be printed up to a certain angle without sagging. To ensure that such overhangs can still be printed, support structures are printed underneath, which are removed after printing.
Types of 3D Printing Technologies
3D printing, also known as additive manufacturing, is a manufacturing process in which objects are built up step by step from individual layers.
Even though the principle in 3D printing is always the same, a wide variety of processes and materials can be used. Either hot material is printed on top of each other, a liquid is cured layer by layer, or sand or powder is liquefied and/or cured layer by layer.
FDM – Fused Deposition Modeling

FDM 3D printing is one of the most widely used 3D printing technologies. In the private sector, it is by far the most popular.
In FDM 3D printing, plastic, or more precisely thermoplastic, is applied as filament through a hot nozzle line by line and layer by layer on a print bed. This makes it possible to realize any geometries, while keeping costs very low and production time short.

An FDM 3D printer consists mainly of a print head that can be moved three-dimensionally in relation to the object. Inside the print head is the so-called hotend, through which the filament is fed and heated. At the end sits the hot nozzle through which the hot and liquid filament is extruded.
The hot filament is applied to a print bed on which it solidifies. After a layer has been applied to the print bed in this way, the print head moves up a bit and prints the next layer on top of the previous one. In this way, the object is successively created from plastic.
However, FDM 3D printers can also print composites such as plastic filament with carbon fibers and pure metal. The latter is particularly interesting for industry, but is far from being as mature and widespread as other manufacturing processes such as turning, milling, stamping, casting or sintering.
In the meantime, there are many inexpensive entry-level 3D printers with which anyone can get a quick and easy start in 3D printing. Also, gone are the days when you had to assemble your own 3D printer from individual parts and you were working more on problems than with printing. Even inexpensive FDM 3D printers are increasingly resembling plug-and-play products that reliably produce objects.
SLA – Stereolithography

In SLA (stereolithography) 3D printing, liquid resin is cured layer by layer by light.
Under a container of liquid resin is a powerful light source, usually in the UV spectrum, which cures the resin after a few seconds. Between the light source and the resin is a thin transparent film that protects the screen.
The print bed starts at the bottom of the resin container and is moved up layer by layer. The first layer is cured on the print bed, the second adheres to the first layer, and so on. This process is repeated for each layer of the object until the final object is completed.

SLA 3D printing is extremely accurate and can achieve layer thicknesses of 0.01 mm with XY resolutions in the range of 20-50 µm. This makes it ideally suited for many industrial sectors and special applications in the private sector. These include jewelry, prototyping or printing of game figures, cosplay equipment and miniatures that can be painted.
The disadvantage of SLA 3D printing is that it usually requires the use of toxic resins. In addition to handling these resins, post-processing of the finished objects is also more costly than with other 3D printing technologies.
Although the resin has already been partially cured during printing, it must be post-cured again after printing by a UV light source. Before that, any resin residue must be washed off, primarily with isopropanol.

With some practice and the right protective equipment such as gloves and respirators, this handling is not a problem and the rework is done quickly, but it deters many beginners.
Overall, SLA 3D printing is a very versatile and common 3D printing technology that is ideal for high-quality and detailed objects. Even inexpensive entry-level SLA 3D printers can now produce smooth surfaces that rival high-quality injection molded parts.
Material Jetting

Material jetting 3D printing has so far only been reserved for larger companies in the industry, as suitable 3D printers cost several $10,000 to $100,000. In return, the possible results through material jetting are very impressive.
In this 3D printing process, various materials are printed in liquid form, similar to an inkjet printer. The great advantage of this process is the high variety of possible materials. Both colored soft and hard photopolymers, wax and edible materials can be printed.
As a result, objects consisting of hard components as well as soft and flexible parts are possible, as shown above. This makes this technology very interesting for a wide range of industries. The more this technology is developed, the cheaper the 3D printers used will become. As a result, the technology will become more and more widespread in the industry and one day print many of our products.
Binder Jetting

B: Binder Jetting printing process where the powder for the next layer is placed either via a hopper or via a roller. (source: sciencedirect.com)
In binder jetting 3D printing, the print head places binder material onto a bed of powder. This powder can be metal, ceramic or sand. The binder glues this powder together to assemble the object.
The major advantages of this 3D printing process are that large objects can be printed relatively quickly and a wide variety of materials can be used for this purpose. Therefore, binder jetting is particularly interesting for industry.

Besides the high cost compared to hobby 3D printing, one of the disadvantages of binder jetting is that the finished parts require complex post-processing to become strong.
Through the printing process, the binder material flows through the powder in a relatively uncontrolled yet accurate manner. On the one hand, this allows relatively detailed geometries to be created, but the surface is usually very rough and porous. Therefore, binder jetting is not suitable for some applications, or the rework becomes even more complex.
Powder Bed Fusion
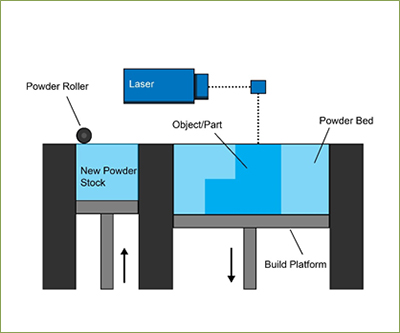
In Powder Bed Fusion 3D printing, a laser melts and bonds plastic, metal or ceramic powder layer by layer to form an object.
Since a laser is used here, the accuracies are very high. Depending on the strength of the laser, a wide variety of materials can also be processed, making this technology suitable for industry, dentistry and other medical fields.
The advantage over binder jetting is that objects made with this 3D printing technology are much more stable. However, the disadvantages are that the process takes much longer and the cost per object increases with the strength of the laser.
This 3D printing method also requires extensive rework to achieve the desired surface quality and material properties.
Sheet Lamination

Although sheet lamination 3D printing can also be done in rudimentary form with paper or cardboard, it is less well known and widespread in the private sector.
In this 3D printing technology, layers of material are bonded together on top of each other, with each layer cut out individually and glued to the last layer. This makes it possible to reproduce relatively complex and precise contours. The resolution depends on the cutting technique and the thickness of the material layers.
The disadvantages of this technique are that the surface quality can be relatively poor and, in the case of metal, can be sharp. In addition, the strength and durability of the object is not comparable to other 3D printing technologies.
Directed Energy Deposition
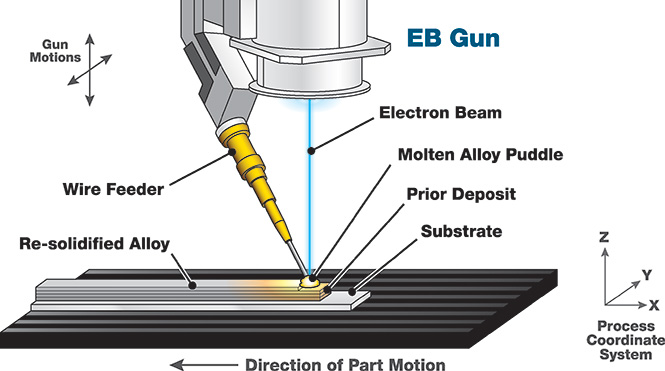
Directed Energy Deposition 3D printing is similar to FDM 3D printing. Only here, instead of being heated and extruded through a nozzle, the material is melted by a powerful electron beam or laser and deposited directly onto the underlying layer.
As you can imagine, this requires industrial-scale equipment. As a result, availability is very limited, requiring a high budget and special training.
However, for anyone with the budget and know-how, using this 3D printing technology can be worthwhile. It can produce highly accurate and very stable objects, which is why this technology is often found in aerospace applications.
In addition to the cost and difficult safety issues, the slow production speed is also a drawback that pushes this 3D printing technology even further into specialized niches.
Materials for 3D Printing
One of the most fascinating aspects of 3D printing is the wide range of materials available. In the private sector, thermoplastic filaments and synthetic resins dominate here. In the professional sector, these are joined by metals, ceramics, sand and various composites.
Thermoplastic

Thermoplastic filaments liquefy when heated and solidify again when they cool. This is the basic principle on which filament FDM 3D printing is based.
The filament is heated in the hot end to the printing temperature, which is usually above 200 °C, extruded through the nozzle and applied to a print bed. There, the filament solidifies, allowing the object to be printed on top of each other layer by layer.

There are many thermoplastics that can be used for 3D printing. The most popular plastics are PLA, ABS, PETG and TPU.
- PLA is biodegradable, cheap and easy to print. On the other hand, it is not as stable as ABS or PETG.
- ABS is strong, impact resistant and also widely used in industry. Among other things, it is often used for electronic housings or toys. However, it is much more difficult to print compared to PLA because it contracts a lot when it cools down.
- PETG is also a strong filament, durable and heat-resistant. Among other things, it is ideal for objects used outdoors.
- TPU is the most popular flexible filament in FDM 3D printing. It has great strength and has special applications due to its flexibility.
In addition to these standard filaments, there are always other thermoplastics that can be used for 3D printing. These include nylon, PP, PC, HIPS and many others. In the industrial sector, even more sophisticated plastics such as PEEK are also used for 3D printing.
Composites

Since most 3D printing processes involve melting and refreezing material, a wide variety of materials can also be combined. Especially in filament 3D printing, composites are therefore very popular.
Here there are many combinations of standard PLA filament with various additives, from wood to metal flakes. Carbon reinforced filaments are also very popular for printing load-bearing parts or those with a mechanical purpose.
There are also many filament types that are combined, such as PC-ABS filament. The two individual filaments are very tough and strong in their own right, but combining them creates an even tougher and harder end product.
The downside to these composites, however, is that they are more challenging to manufacture. In particular, hard additives such as metal flakes or stone powder can quickly wear out soft nozzles. If you plan to print frequently with such filaments, I would advise you to use a harder and larger nozzle.
Resin

Resins produce extremely accurate surfaces. Because the SLA 3D printing process is relatively inexpensive to implement, resin 3D printers are also very common and popular in private homes.
Resins for 3D printers are made of polymers that crosslink and cure more strongly when energy (usually UV light) is applied. Since light can be positioned very precisely, even tiny pixel sizes can be implemented.
While there are also a wide variety of resins with different properties, the material selection is nowhere near as large as in filament FDM 3D printing. In addition to standard resins, there are also water-soluble resins, ABS-like resins, transparent materials, and resins designed for resolutions of 8K and higher.
The downside to resin, however, is that it is toxic. At least in its liquid state, it irritates the skin, respiratory tract and is toxic if swallowed. Only when cured, it is safe to touch and further work on the object.
Moreover, the fumes produced when printing resin objects are toxic. Therefore, it is essential to wear appropriate personal protective equipment when handling synthetic resins and ideally to avoid the room in which printing is taking place and to ventilate well after printing.
Metal

Fast, cost-effective, simple and stable FDM 3D printing with metal is the holy grail of the manufacturing industry. However, metal 3D printing is still reserved for certain niches where complex components need to be best made from one piece and price is irrelevant.
While there are already more affordable metal FDM 3D printers (e.g. from Ultimaker), printing objects with a smooth surface and a stable structure is not yet suitable for the masses.
In principle, FDM 3D printing with metal works the same way as with plastic. The metal is melted, deposited in layers and solidified. The obvious advantage is that objects made of metal are much stronger than those made of plastic or resins. The disadvantage is the high cost.
However, metal can also be processed as powder in 3D printing.
Powder
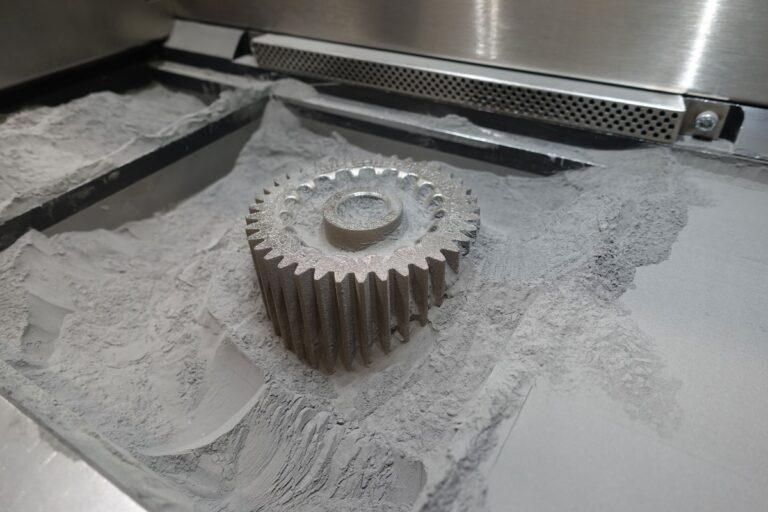
The powder, which can be used for 3D printing, can consist of metal, ceramics or plastics. Therefore, a wide variety of applications are also possible with this type of material.
The main 3D printing processes that use powder include Binder Jetting, Direct Energy Deposition and Powder Bed Fusion (see above).
The use of metal powders in 3D printing is particularly common in the aerospace, medical and automotive industries, as they can be used to quickly produce complex objects from a single piece.
Applications of 3D Printing
Due to the wide range of materials, the rapid production of parts and the realization of special geometries, 3D printing has many possible applications.
There are many more applications for 3D printing in addition to prototyping to mass production in the professional sector and in the private sector for hobby and art.
Hobby


3D printing allows hobbyists to realize creative ideas with a wide variety of materials and almost any level of detail. Also, the practical use for spare parts or other home improvements is very popular.
Making products in your home is very appealing to many users, as it reduces delivery times and costs, and often allows more freedom than buying finished products.
It has also become increasingly easy to get started in the 3D printing hobby, as even inexpensive entry-level 3D printers continue to improve and deliver reliable results.
Due to the ease of entry and widespread use of 3D printing in the private sector, there are large communities in which 3D objects are exchanged and traded. This also allows users to print objects without ever having to use a CAD program.
Prototyping in Design and Industry

In the later stages of product design, prototypes need to be made to test geometry and functions. So that all manufacturing processes don’t have to be already developed for this, 3D printing offers a fast way to test these product features within hours.
Since FDM 3D printing in particular is fast and inexpensive, the product can be printed immediately as soon as a CAD version of the product is available. This accelerates the development of complex objects because the geometry can be tested directly and errors can be detected sooner.
The time that elapses between the idea and the release of the product is greatly reduced by the rapid prototyping that 3D printing provides.
Consumer Product Manufacturing

The unique capabilities of 3D printing are also widely used in the manufacturing of consumer goods. In particular, the speed and flexibility of 3D printing is very appealing to manufacturers who produce many small batches.
To avoid having to restructure the entire manufacturing process for each new product, a 3D printer can simply be fed a new CAD file.
However, most consumer products are still made using traditional manufacturing methods such as injection molding or metal milling. It will be a long time before 3D printing becomes dominant in the market, if it even gets that far. To ensure that 3D printing does not remain a niche technology in the industry, the accuracy of some processes and the resulting stability of the object must be increased and costs reduced.
Automotive

For a long time, the sole purpose of 3D printing in the automotive industry was to produce tools for manual production and prototypes for development. Now, however, the quality of 3D-printed parts is so good that they can be used in the final product.
A major advantage related to this is the logistics of spare parts. Every car manufacturer has to keep spare parts for at least ten years. Depending on how many spare parts there are and how many cars are in circulation, the storage and production of these spare parts can be expensive.
If at least some of them are 3D printable, these spare parts can be printed when needed. This makes storage costs almost non-existent.
Aviation

Manufacturing parts for aviation is very costly, as this type of manufacturing is subject to strict rules and certifications. So, any kind of cost reduction is very welcome for most manufacturers, as long as all safety aspects and functions are given.
Therefore, 3D printing is often used in the aerospace industry for simple parts like air ducts or other small plastic parts.
But as in many other industries, 3D printing is often used in the aerospace industry for prototyping. Miniaturized prototypes of aircraft can be used to quickly test their aerodynamic properties and design concepts.
Education
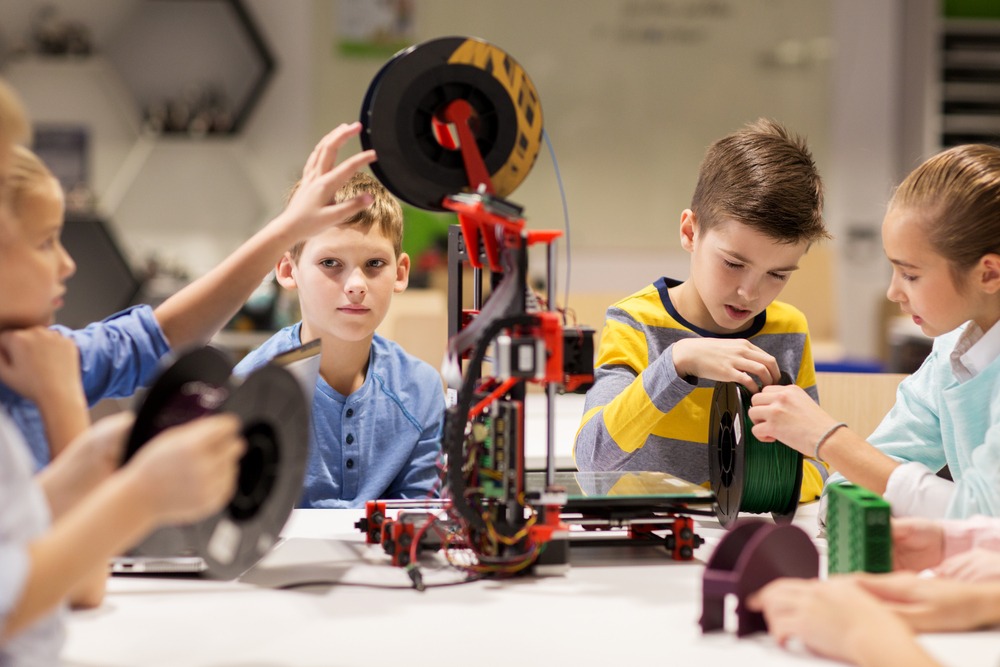
In today’s society, it’s no longer enough to just teach children how to use languages and math. Modern technology must also be learned at an early age. 3D printing is ideal for this, as it teaches both the physical handling of manufacturing techniques and how to operate and program them using a computer.
But even at universities for architecture, mechanical engineering or product design, a 3D printer can help students realize their ideas and digital objects.
Medicine
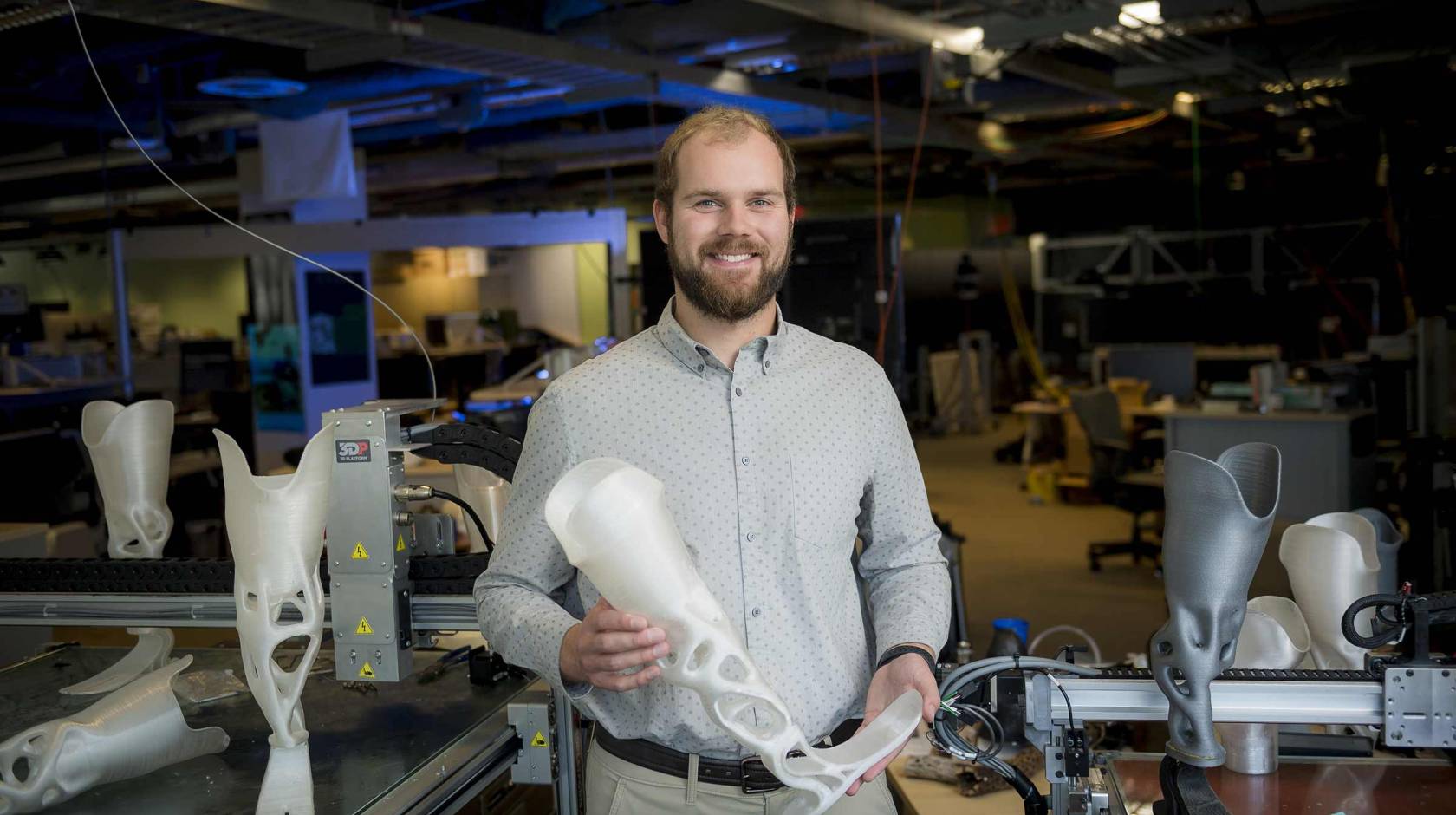
Due to the flexibility of 3D printing and the ability to produce complex objects from a single piece, 3D printing is widely used in medicine. It is applied here for customized prosthetic limbs, anatomical models, robotic surgical instruments, and patient-specific models for surgery planning.
Construction
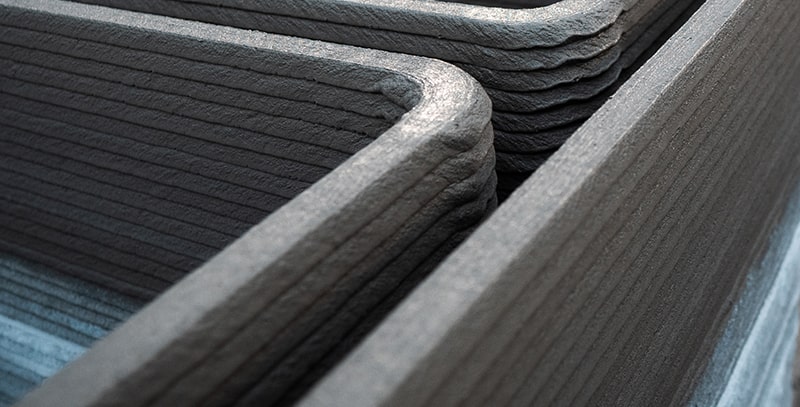
There are now already the first buildings that were mostly 3D-printed. The process is based on FDM 3D printing and prints the walls of the house layer by layer of concrete.
Manufacturers of such buildings promise a faster, safer and more stable construction of these houses at a lower cost.
Also, this principle has already been brought into the conversation for the construction of a Mars base, as the building material can be mixed directly on site and a robot can print the houses autonomously.
Food

Just like thermoplastics, there are also foods that are liquid at high temperatures and solidify at room temperature. For example, chocolate can also be printed. With an oven, pastries can also be printed in complex structures.
It will be exciting when real meat can be printed. So far, there are companies 3D printing meat-like products, but these are often based on plant-based materials.
Fashion

3D printing hasn’t really arrived in the fashion industry yet. However, there are many designers who are using it to bring creative ideas to life. While most of these ideas are more extravagant than practical and would break immediately in everyday use, there are also interesting combinations of hard plastic incorporated into fabric.
Architecture

As in many manufacturing industries, 3D printing is used in architecture for prototypes and models. Concept designs can be quickly tested and presented. It often helps to hold the designed object in hand to discover improvements and flaws.
Jewelry
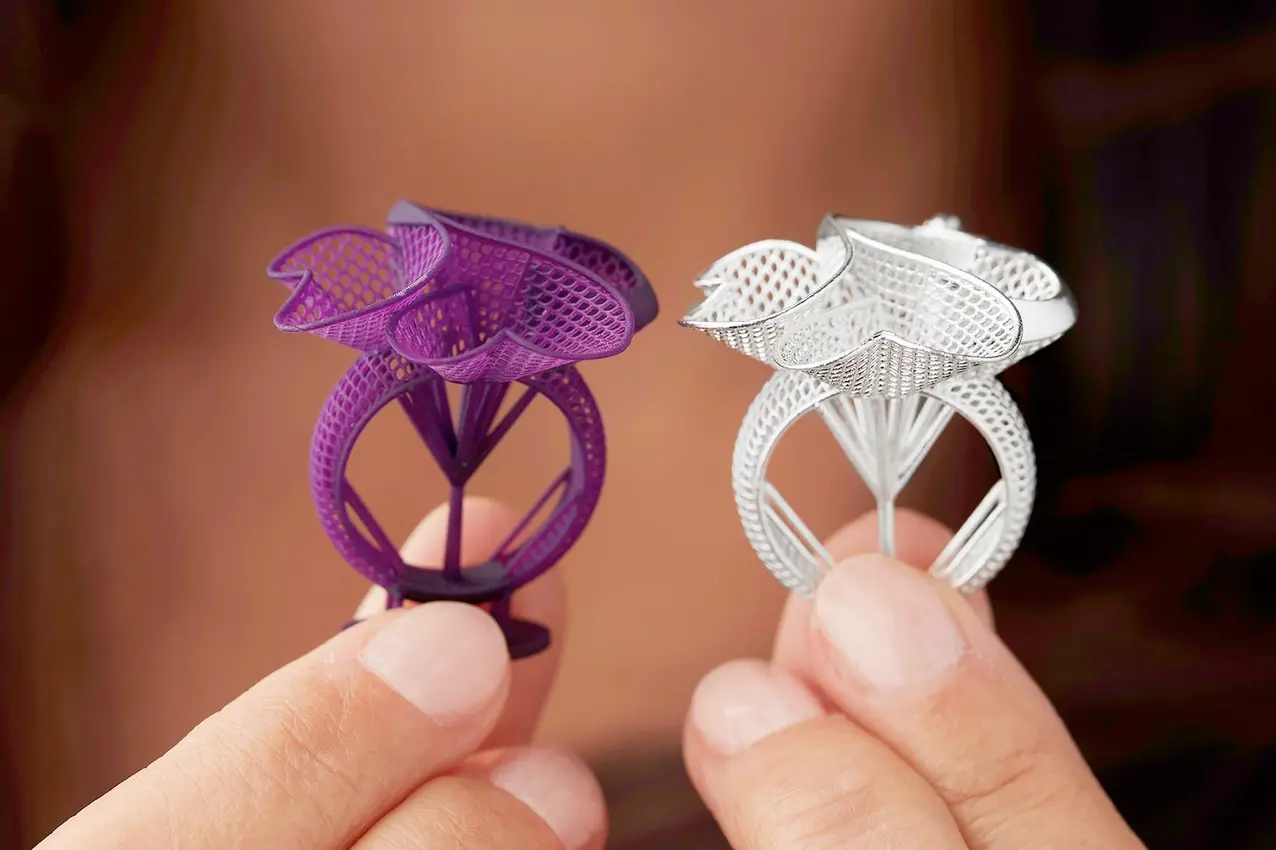
In jewelry art, the high-precision SLA 3D printing is mainly used. This can be used to produce very fine and complex objects, some of which cannot be produced using traditional methods.
Often, a prototype is printed here from synthetic resin, a negative mold of which is produced, which can then be flooded with metal.
Conclusion
3D printing is a revolutionary technology. It has developed rapidly in recent years and has many fans not only in industry but also in the private sector.
3D printing makes it possible to create more flexible productions and produce geometries that would not be possible with other methods.
I hope this article has inspired you to learn more about 3D printing. Whether you are a hobbyist, a professional or just curious, the world of 3D printing is waiting for you to discover it!
Disclosure: This website is the property of Martin Lütkemeyer and is operated by Martin Lütkemeyer. Martin Lütkemeyer is a member of the Amazon Services LLC and other Affiliate Programs. These are affiliate advertising programs designed to enable websites to earn advertising revenue through advertising and linking to Amazon.com and others. Links marked with * are affiliate links.